Solving the Material Management Chaos in Configurators
- Abhay Sharma
- Feb 24
- 2 min read
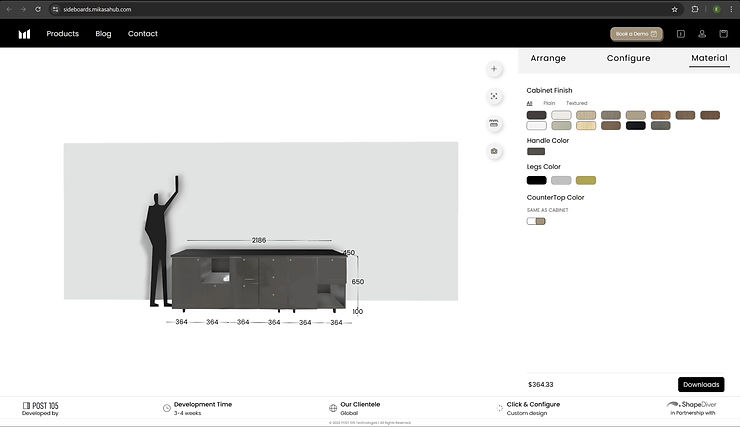
Ever struggled with outdated or inconsistent materials in 3D configurators? Manufacturers and sellers face this daily challenge when trying to provide seamless customization options. While 3D configurators are essential for manufacturers and sellers—allowing customers to view products in real time, customize designs, and make informed purchasing decisions—one major hurdle remains: managing and accessing the diverse materials used in production.
Each manufacturer maintains unique material libraries, making synchronization with configurators complex and inefficient. This challenge affects not only manufacturers but also configurator developers and designers, leading to inconsistencies, redundant work, and higher maintenance costs.
The Problem: Fragmented Material Management
Right now, manufacturers are keeping their materials in separate databases or unique systems. This fragmentation leads to several challenges:
Inconsistent Data: Different suppliers use various formats and classifications, making it tough to standardize.
Redundant Effort: Each configurator has to manually gather and combine material info from each manufacturer.
Limited Accessibility: Vendors often have to update materials in several places, adding complexity and the risk of outdated info.
Integration Challenges: Linking different material libraries with various configurators requires custom work, slowing down the design process.
The Solution: A Centralized Material Database
A centralized material database simplifies the process by providing a single platform where vendors and manufacturers can upload, manage, and share materials effortlessly. This database connects with various 3D configurators through a standardized API, ensuring easy access and integration.
Key Benefits of a Centralized Database
Simple Material Upload: Vendors can easily upload material textures, specifications, and details using a user-friendly web platform.
Smart Categorization: Materials can be sorted by type, texture, manufacturer, or use.
API Access: Configurators can fetch material data via API calls, ensuring they always have the latest information.
Easy Updates: Manufacturers can tweak or update materials without needing to manually notify each configurator.
Secure & Scalable: The platform keeps materials safe and allows controlled access for different users and manufacturers.
How It Works
Manufacturers Upload Materials: Vendors log into the platform and upload material images (textures) with details like size, color, and reflectivity while the platform validates and stores the materials neatly.
Configurators Fetch Materials: A configurator requests materials from the database via API and filters results by category, manufacturer, or texture type.
Real-Time Updates & Synchronization: When manufacturers update or add materials, configurators receive the latest data automatically.
The Results
Efficiency & Automation: Eliminates manual work so manufacturers can focus on design and production.
Improved User Experience: Configurators offer a better selection of materials for designers and customers.
Consistency Across Platforms: Standardized data ensures all configurators display materials accurately.
Time & Cost Savings: Reduces repetitive data entry, lowering development and maintenance costs.
Scalability: A growing vendor network enriches the material ecosystem for manufacturers and designers.
Ready to Transform Material Management?
Want to simplify material management and improve configurator efficiency? Reach out today to explore seamless integration!
Comments